The HST series hydraulic cone crusher is a high efficiency cone crusher designed by introducing American technology and combining the metal nature on the world market. It is widely used in metal mine, metallurgical, chemistry, construction, cement, sand and stone production industry. It applies to the primary and secondary crushing of various of mines and rocks, the Protodyakonov hardness of which is f=5-16, such as iron ore, nonferrous ore, granite, limestone, quartzite ore, sandstone, pebble and so on.
Features:
1.High efficiency: The hydraulic cone crusher has support on both ends of the spindle, which is able to bear greater crushing force and greater stroke, coupled with the special shape of crushing chamber adapted to laminated principle, the machine has higher crushing efficiency.
2.Large production capacity: The hydraulic cone crusher has the perfect combination of design with crush stroke, crushing speed and crushing chamber shape, which make the machine's moving cone big end diameter in the same circumstances, the output is 35% ~ 60% higher than the old spring cone crusher.
3.High quality stones: The hydraulic cone crusher adopt special crushing chamber and laminated crushing principle, resulting in inter-particle crushing effect, so that the finished product significantly increased the proportion of the cube, flake stone needles reduced and grain is more uniform.
4.Just replacing the fixed cone can achieve a variety of cavity shapes for fine crushing.
5.Double insurance controlled hydraulic and lubrication system can ensure the machine's overload protection and good bearing lubrication.
6.Easy maintenance: The structure of cone crusher is simple and compact.It has the features of stable performance, not easy to fault and convenient maintenance.
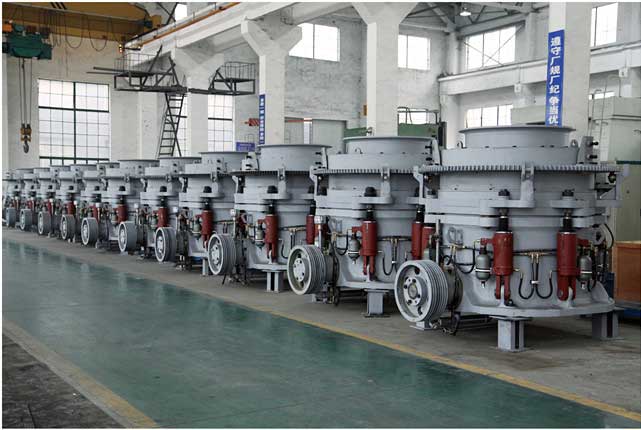
Working principle
The electromotor leads the eccentric sleeve to rotate by the V-belt, drive shaft and drive gear. The movable cone does rotary and pendulum movement under the leading role of eccentric sleeve which makes the movable cone and fixed cone close and far away from time to time. The raw material is crushed in the crusher chamber by squeezing and striking continuously. The crushed stone discharges from the bottom.
DATA
Model |
Cavities |
Maximum feeding size(mm) |
Minimum discharging size(mm) |
Maximum install power(kW) |
HST100 |
S1 Extra Coarse |
240 |
22 |
90 |
S2 Medium Coarse |
200 |
19 |
H1 Fine |
135 |
10 |
H2 Medium Fine |
65 |
8 |
H3 Extra Fine |
38 |
4 |
HST160 |
S1 Extra Coarse |
360 |
25 |
160 |
S2 Medium Coarse |
300 |
22 |
S3 Coarse |
235 |
19 |
H1 Fine |
185 |
13 |
H2 Medium Fine |
90 |
10 |
H3 Extra Fine |
50 |
6 |
HST250 |
S1 Extra Coarse |
450 |
35 |
250 |
S2 Medium Coarse |
400 |
29 |
S3 Coarse |
300 |
25 |
H1 Fine |
215 |
16 |
H2 Medium Fine |
110 |
13 |
H3 Extra Fine |
70 |
8 |
HST315 |
S1 Extra Coarse |
560 |
41 |
315 |
S2 Medium Coarse |
500 |
38 |
H1 Fine |
275 |
16 |
H2 Medium Fine |
135 |
16 |
H3 Extra Fine |
65 |
13 |